NL
Het is het eerste voorbeeld van een
succesvolle samenwerking door een
gemotiveerd team: Christoph
Nussbaumer (onze Oostenrijkse
ontwerper), Potito Cordisco en Mauro
Terraneo (luchtvaartingenieurs),
Marco en Dino Merelli
(koolstofvezelingenieurs), alle
betrokken leveranciers met hun
werknemers en ons team in het
hoofdkantoor. Dankzij de evolutie
van composietmaterialen is deze
versie volledig "verfvrij". De
technische prestaties zijn veel
verbeterd, dankzij de aanpak van een
ander materiaal (twee
visco-elastische dempers zijn nu
verkrijgbaar in elke doos, dubbele
ontkoppelingsringen verbinden carbon
frame met structuur en verstelbare
voeten hebben nu een nieuw elastisch
materiaal). Dankzij een nieuwe vorm
en een compleet ander lamineerproces
(monodirectionele en bidirectionele
koolstofvezelhuiden werken samen) is
de torsie van het carbonframe met
ongeveer 85% verminderd in
vergelijking met de vorige versie.
Nieuwe materialen zoals 3D Core
(gebruikt door Lamborghini, Aston
Martin, BMW M en nog veel meer)
bevinden zich in de zwevende plank
en helpen trillingen te verwijderen
die worden gegenereerd door motoren
van draaitafels en cd-spelers. Op
aanvraag kunnen enkele kleine
details worden aangepast.
English
It is the first example of a
successful cooperation by a
motivated team: Christoph Nussbaumer
(our Austrian designer), Potito
Cordisco and Mauro Terraneo (aeronautical
engineers), Marco and Dino Merelli
(carbon fibre engineers), all the
involved suppliers with their
workers and our team in the HQ.
Thanks to the evolution of
composites materials, this version
is completely "paint free".
Technical performance has been
improved a lot, due to a different
material's approach (two
visco-elastic dampers are now
available in any box, double
decoupling rings connect carbon
frame with structure and adjustable
feet have now a new elastic material).
Thanks to a new shape and a
completely different lamination
process (mono-directional and
bi-directional carbon fibre skins
are working together), carbon frame
torsion has been reduced about 85%
compared with previous version. New
materials like 3D Core (used by
Lamborghini, Aston Martin, BMW M and
many mores) is inside of the
floating shelf and helps to
dissipate vibrations generated by
turntable and CD players engines. On
demand a few small details can be
customized. REVOLUTION X.
A visionary project started in 2020:
improve a series of objects that
have been a benchmark for almost
seven years in the world of premium
racks. The evolution of composite
materials technology, the creative
genius of Christoph Nussbaumer, a
team of experienced technicians and
engineers and our long-time
experience in the fight against
vibration, made it possible to
create products that were
unthinkable until a few years ago.
After almost two years of research
and hard work we are proud to
present a new benchmark: REVOLUTION
X. WE WILL RACK
YOU - Revolution Line becomes
Revolution X
We like to explore different worlds
and ways of thinking. We think that
rooting your work on outdated
concepts limits the evolution and
prevents new discoveries from being
made. Since ever we go against the
tide, from the begining we have been
innovators and architects of our
destiny. Leaving the tracks traced
by preconceptions it’s often risky
but we love challenges. Revolution X
represents the best we have been
able to create until today. A
totally inert rack over 114 Hz with
elevated muffling peaks already at 7
Hz. All measured and measurable, all
certified by a totally independent
analysis laboratory.
Christoph Nussbaumer - Inspired
by technology
Austrian-born with roots in a
artisans family he graduated at
Scuola Politecnica di Design. He
collected experiences in
international design-agencies in
Salzburg, Milan and Boston. In 1997
he founds and directs one of most
successful innovation driven italian
ID-agencies. His team of designers
and engineers wins over 200
international design and industry
awards.
Currently he leads a small and
flexible, highly specialized design
& engineering team, offering
innovative design-solutions. His
studio has a prestigious client
portfolio such as Scarpa, Atomic and
Smeg. Specialist in applied
ergonomics, sports biomechanics and
brand strategy, Christoph’s work is
inspired by technology.
CARBON IS CLEARED TO TAKE OFF -
Monocoque technology
Back in 2015 we were the first to
introduce on the market a rack in
structural carbon: to this day no
one was able to imitate it. In 2022
we launch on the market an object
that demolishes and revolutionizes
completely everything that shocked
us at the time. The apparent
stiffness of the monocoque frame
actually hides a flexible soul which
makes of AEON X the new benchmark on
the market. We use the same
monocoque technology of the F1
safety cells. The structural overlap
in the lamination process ensures
reduction of peripheral torsion,
resistance to static load, low
frequency vibration damping.
Everything is summed up in a
performance never measured before in
only 1,7 mm of carbon fibre.
THE ONLY WAY TO TEST - Testing
process
As always, once again we are not
improvising. All our racks undergo a
precise test protocol (static and
dynamic). Understanding and
measuring what happens to our
products, allows us to ensure that
they really work. Incremental static
load tests and modal analysis
conducted with 28 accelerometers (mono-axial
and triaxial) provided us data to
optimize the densities of damping
materials and the laminating
processes of the carbon fibre. All
the reports can be downloaded
directly from our website. The main
purpose of a rack is to isolate the
electronics from vibrations that
negatively affect their performance:
our racks are doing this, Revolution
X does it even better! Carbon look,
listening test, anti-resonant paints,
“tuned” by ear shelves and other
similar sentences, represents
garbage that does not belong to us.
You would never drive your super car
with the tires of a small car. Place
your electronics only on racks that
guarantee you measurable
performance.
FLAGSHIP CARBON FIBER AV RACK
Argo X is a rack provided with a
carbon fiber monocoque, produced
with the same technology of the
safety cells used in F1. The
structural overlap in the lamination
process ensures reduction of
peripheral torsion, resistance to
static load, low frequency vibration
damping. Everything is summed up in
a performance never measured before
in only 1,7 mm of carbon fibre.
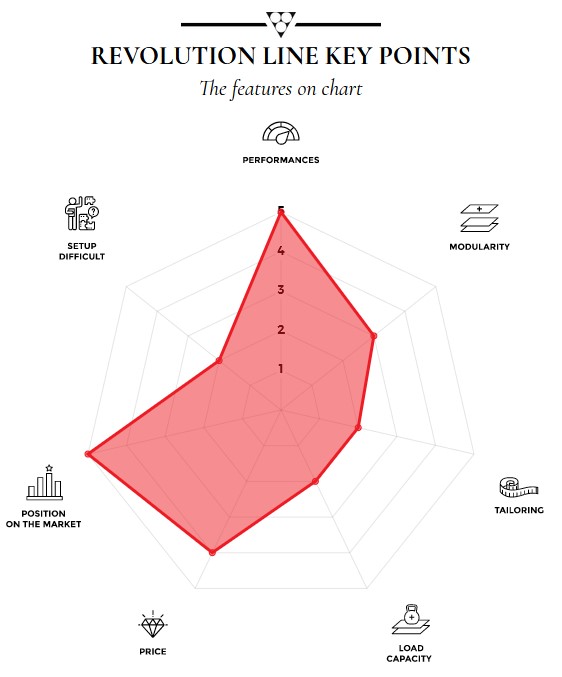
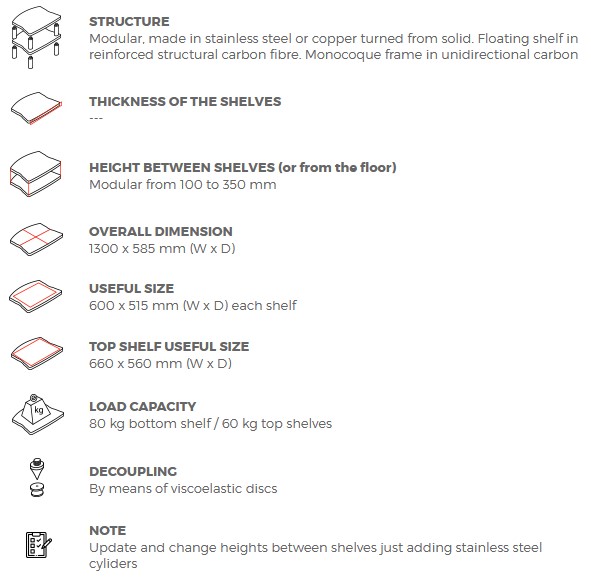 |